
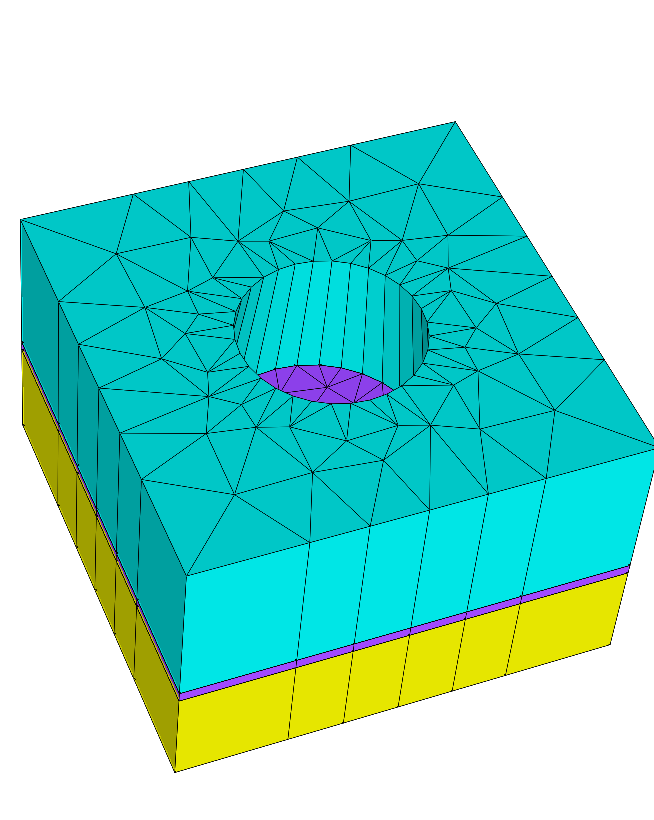
In this research, a method was proposed to generate tool paths for the machining of complex spherical surfaces based on an ultra-precise five-axis turning and milling machine with a C-Y-Z-X-B structure. However, the geometric shapes of workpiece surfaces cannot be adequately manufactured with simple plane, cylindrical, or spherical surfaces because of their different applications in various fields. The improvement of ultra-precision machining technology has significantly boosted the demand for the surface quality and surface accuracy of the workpieces to be machined. This would help in building the performance of athletes in the game. We further developed an idea that could also be used to determine the trajectory of a dual-axis spinning ball. The integration of spin in the simulation also yielded results that showcased the Magnus effect, this visualization is generally not observable on experimental methods since it involves complex processes to simulate spin, hence the trajectory of balls under different shots and pitches has been observed. By observing the values of lift and drag coefficients we can validate computational results with experimental results obtained from reference journals, thus proving that computational simulation has a place in predicting the trajectory and behaviour of moving balls in real-time. A moderate value of surface roughness was given to model the effects of change in the surface between the two balls and the delay in boundary layer separation subsequently affecting the distance travelled by the ball was seen. For the inlet, different values of velocity based on the motion of the ball in the game were given. The basic conservation equations in fluid dynamics are applied to the domain of study to plot the results. Most realistic initial and boundary conditions are used to simulate each type of ball and to identify key design aspects that can be applied and modified to enhance the performance of the ball and hence improve the game. The objective of the project is to determine the aerodynamic characteristics of baseballs and tennis balls using Computational Fluid Dynamics (CFD) methods. The method could be applied to complex spherical surfaces with other characteristics. The presented tool path generation method in this research produced ultra-precision spherical complex surfaces. Furthermore, the surface roughness within the spherical region appeared to be less than 30 nm.

The surface roughness of the machined workpiece was less than 90 nm. Based on an ultra-precision three-coordinate measuring instrument and a white light interferometer, the machining accuracy of a workpiece surface was characterized, and the effectiveness of the tool path generation method was verified. Then the tool paths were generated with a numerically controlled (NC) program. First, the complex spherical surface model was modeled and calculated, and then it was combined with the designed model to generate the tool path. Through the proposed tool path generation method, ultra-precise complex spherical surface machining was achieved.
